Prototype Mold Makers Manufacturers: Pioneering Innovation in Metal Fabrication
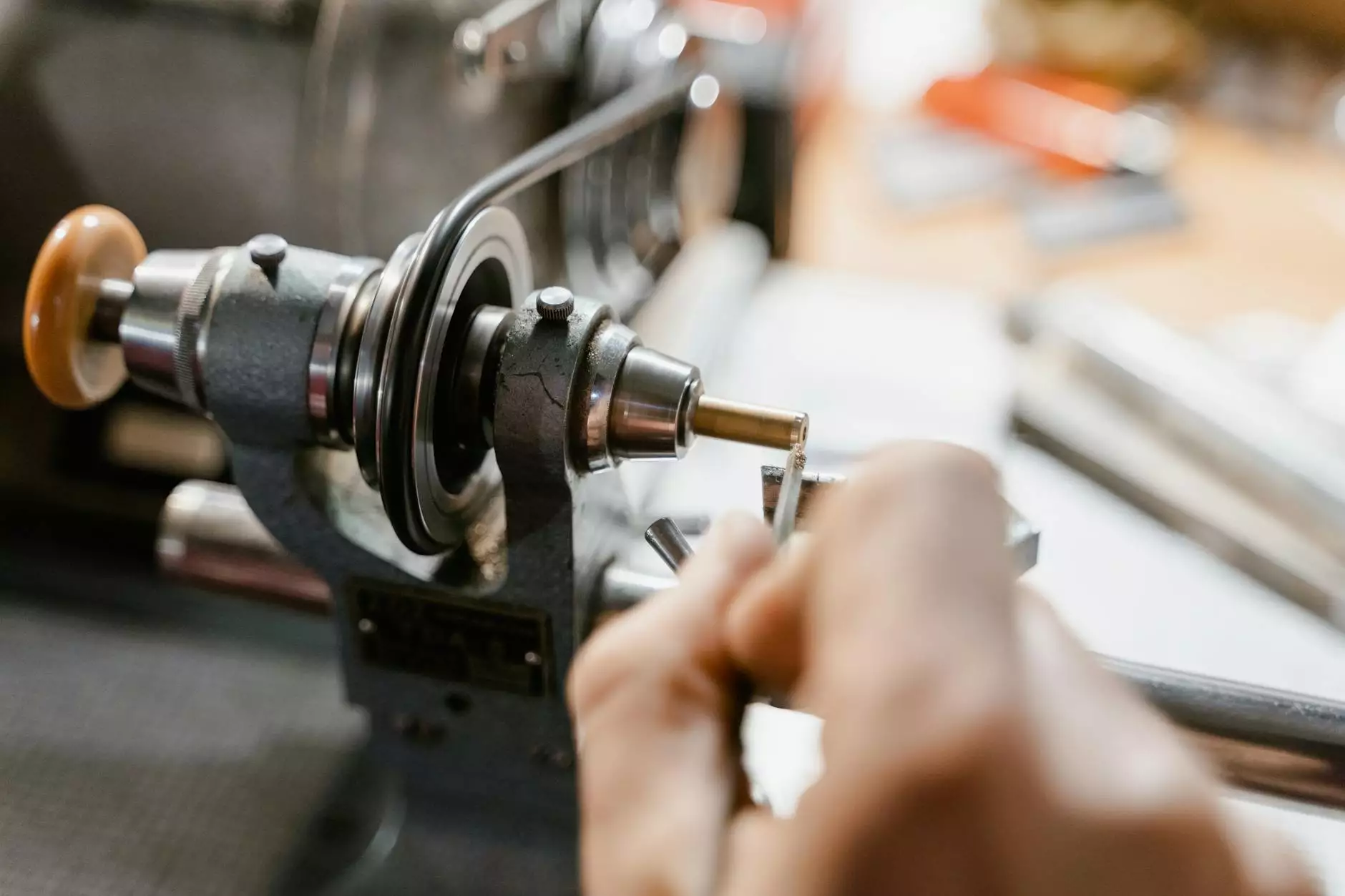
In the vast landscape of modern manufacturing, prototype mold makers manufacturers play a crucial role, bridging the gap between ideas and tangible products. As industries continue to evolve, the demand for precision, quality, and speed in product development has never been higher. This article delves into the intricacies of what makes these manufacturers vital to the success of various sectors, particularly in the realm of metal fabrication.
Understanding the Role of Prototype Mold Makers
Prototype mold makers are specialists who design and create molds used to produce parts and products through processes like injection molding, blow molding, and compression molding. Their expertise not only lies in crafting these molds but also in ensuring they meet the specific needs of their clients, which may range from automotive to consumer goods.
The Importance of Prototyping in Manufacturing
Prototyping serves as a critical step in product development. It allows manufacturers to test and refine their designs before committing to full-scale production. This practice helps identify potential issues early, saving time and costs in the long run. Here are some reasons why effective prototyping is essential:
- Early Detection of Flaws: Prototypes allow designers and engineers to spot design flaws before mass production, ensuring quality control from the outset.
- Cost Efficiency: Investing in prototypes can drastically reduce production costs by eliminating the need for expensive modifications during mass manufacturing.
- Enhanced Product Development: Prototyping encourages innovation, enabling teams to explore multiple design variations and select the best solution.
The Process of Mold Making
The process of mold making involves several steps, each critical to the success of the final product. Here’s a detailed look at the steps involved:
1. Design and Engineering
The initial phase involves the creation of a design based on specific product requirements. Engineers utilize CAD (Computer-Aided Design) software to create digital blueprints that outline dimensions, materials, and functional features of the mold.
2. Material Selection
The choice of material for the mold greatly influences its durability and performance. Commonly used materials include:
- Steel: Known for its strength and longevity, steel molds are ideal for high-volume production.
- Aluminum: More affordable and easier to machine than steel, aluminum molds are great for low-volume runs or prototypes.
3. Machining
Once the design and materials are finalized, the machining process begins. This involves precise cutting, milling, and grinding to shape the mold components accurately.
4. Assembly and Testing
After machining, the mold components are assembled. The assembled mold undergoes rigorous testing to ensure it meets design specifications and functions perfectly.
Advancements in Mold Making Technology
With rapid advancements in technology, the mold-making industry is experiencing significant transformations. Innovations such as 3D printing, CNC machining, and advanced materials are reshaping traditional practices. Some of the latest trends include:
1. 3D Printing
3D printing technology has revolutionized prototype mold makers manufacturers by enabling rapid prototyping and quicker iterations of designs. It allows for more complex shapes and lightweight structures that were previously unattainable with traditional methods.
2. Smart Manufacturing
Smart manufacturing integrates IoT (Internet of Things) and AI (Artificial Intelligence) into the mold-making process, improving efficiency and reducing downtime. These technologies enable real-time monitoring and predictive maintenance of machinery.
3. Advanced Materials
Innovation in materials science has led to the development of high-performance materials that can withstand extreme conditions. These materials not only extend the lifespan of molds but also enhance the quality of the produced parts.
Choosing the Right Prototype Mold Makers Manufacturers
Selecting the right manufacturer is pivotal to ensuring the success of your project. Here are some factors to consider:
- Experience and Expertise: Look for manufacturers with extensive experience in your specific industry and a proven track record of delivering quality molds.
- Technological Capabilities: Choose manufacturers that leverage the latest technologies and methodologies in mold making, such as 3D printing and CNC machining.
- Customer Service: A responsive and knowledgeable support team is vital for addressing any concerns and ensuring smooth communication throughout the project.
- Quality Assurance: Ensure they have stringent quality control processes to maintain high standards in mold production.
The Impact of Metal Fabrication in Various Industries
Metal fabrication, closely intertwined with mold making, is a foundational aspect of many industries. Its applications are vast and varied, including:
1. Aerospace
The aerospace industry demands precision and reliability. Fabricated metal parts are critical for aircraft manufacturing, ensuring safety and performance at high altitudes.
2. Automotive
In the automotive sector, metal fabrication is essential for producing components such as chassis, body panels, and engine parts. The efficiency of prototype molds can significantly impact the production timeline and costs.
3. Consumer Products
The consumer goods market relies heavily on metal fabrication for a variety of products. From kitchen appliances to electronics, having reliable molds enhances the manufacturing process.
Conclusion: The Future of Prototype Mold Makers Manufacturers
The prospects for prototype mold makers manufacturers are brighter than ever. As industries continue to advance and evolve, the need for innovative solutions in mold making will increase. By embracing cutting-edge technology and adapting to market demands, these manufacturers will remain at the forefront of the manufacturing landscape.
In conclusion, choosing the right prototype mold makers is essential for any manufacturer looking to excel in their respective industry. With the right partner, businesses can navigate the complexities of product development, ensuring they stay competitive in a fast-paced market. For those seeking excellence in metal fabrication, DeepMould.net stands ready to offer unparalleled services, helping transform ideas into reality.